技術紹介
当社の独自技術であるIon Assist蒸着法(IAD)は原料を電子ビームで加熱溶融して真空中で蒸着させます。同時に酸素イオンを基盤に照射(1kV)して緻密な成膜を形成させます。原子レベルで成膜するので緻密で硬い膜ができ、クリーンな環境で成膜できます。形成された膜は研磨不要です。
当社の独自技術であるIon Assist蒸着法(IAD)は原料を電子ビームで加熱溶融して真空中で蒸着させます。同時に酸素イオンを基盤に照射(1kV)して緻密な成膜を形成させます。原子レベルで成膜するので緻密で硬い膜ができ、クリーンな環境で成膜できます。形成された膜は研磨不要です。
Ion Assist蒸着法とは
つばさ真空理研株式会社は、特殊なIon Assist蒸着技術によって気孔のない、非常に緻密な酸化イットリウム( Y₂O₃ )膜を形成することを特徴としています。耐食性保護膜によってパーティクルを低減させ、生産性の向上、製品の信頼性向上につなげていきます。次世代技術として酸フッ化イットリウム(YOF)やYAG(Al₃Y₅O₁₂)にも取り組んで開発していきます。
従来の溶射による成膜では粉体をプラズマで半溶融状態にして照射させる成膜法なので緻密な膜ができない問題点があります。Ion Assist蒸着は原子状態で成膜し、酸素イオン照射で膜を緻密化させますので原子レベルで緻密な膜ができます。
従来の溶射による成膜では粉体をプラズマで半溶融状態にして照射させる成膜法なので緻密な膜ができない問題点があります。Ion Assist蒸着は原子状態で成膜し、酸素イオン照射で膜を緻密化させますので原子レベルで緻密な膜ができます。
特殊なIon Assist蒸着法により
形成した気孔の無い 非常に緻密なY₂O₃膜 |
||||
↓
|
||||
Etching装置
PE-CVD装置 |
→
|
F耐食性保護膜
御提案Y₂O₃ |
→
|
パーティクル
低減 |
原子レベルでの成膜
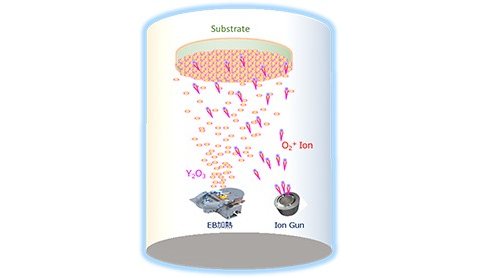
原子レベルでの成膜
イオンアシスト蒸着(IAD)
分子状態で成膜+酸素イオン照射で緻密化原子レベルで緻密な膜が出来る
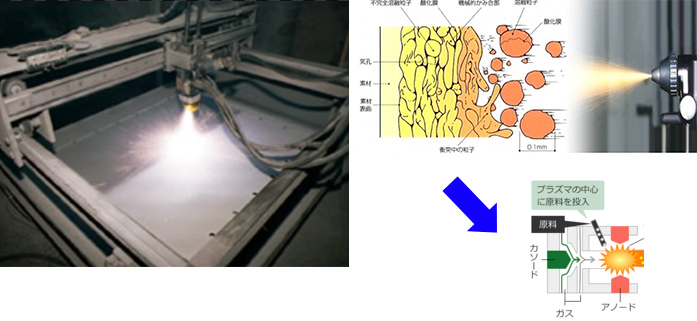
真空成膜で初めて10μm以上成膜成功=気孔のない緻密膜
従来の溶射成膜(APS)
粉体をプラズマで半溶解状態にして照射厚膜には良いが緻密にならない
真空成膜で初めて10μm以上成膜成功=気孔のない緻密膜
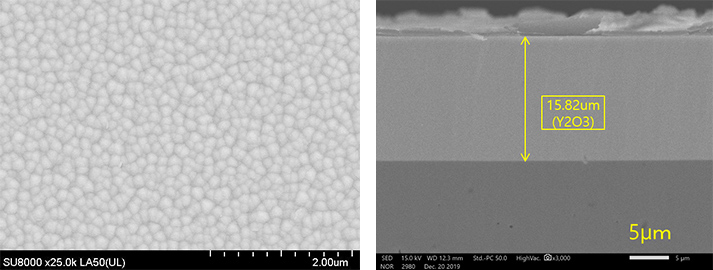
原子レベルでの成膜
イオンアシスト蒸着(IAD)
非常に緻密な膜→パーティクル低減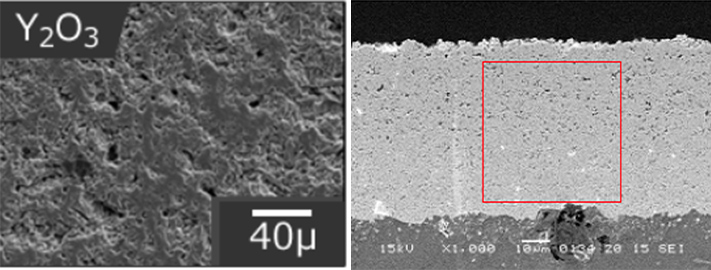
真空成膜で初めて10μm以上成膜成功=気孔のない緻密膜
従来の溶射成膜(APS)
気孔が多い膜→パーティクルの原因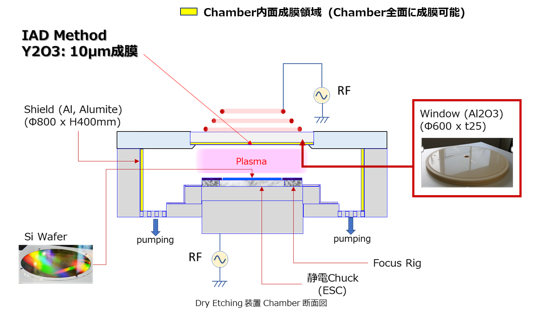
ドライエッチング装置、プラズマCVD(PECVD: Plasma-Enhanced Chemical Vapor Deposition)装置における表面保護膜には緻密性と耐プラズマ性が求められます。耐プラズマ性に優れたセラミックス材料としては、 Y₂O₃ 、YOF、 YAG といった希土類酸化物またはフッ化物が有効です。イットリウムを含む希土類酸化物が耐プラズマ性に優れるのは、フッ素プラズマに基材が暴露した際、酸化アルミニウム(Al₂O₃)はAl表面がフッ化しフッ化アルミニウム(AlF)を形成しAlFは生成自由エネルギーがマイナスレベルで小さく揮発しやすいことでパーティクルの原因になります。 Y₂O₃ 、YOF、 YAG等のイットリウム酸化物については、表面のイットリウムがフッ化することによりフッ化イットリウム(YF₃)となりますが、生成自由エネルギーがマイナスレベルで大きく質量が大きいため揮発せず表面に残留するのでこれが耐プラズマ性向上の要因と推測されます。フッ素プラズマ照射後のY₂O₃やYOF(オキシフッ化イットリウム)セラミックスの断面SEM画像では、Y₂O₃セラミックスの表面にわずかな濃いコントラストの変質層が観察されたのに対してYOFセラミックスの表面はフッ素プラズマ曝露後に変化はありませんでした。弊社は二元同時蒸着を行うことで酸素とフッ素の比率を自由に制御して緻密なYOF膜を形成することができます。チャンバ部品におけるセラミックス膜の耐プラズマ性向上及び緻密化は歩留まり向上とメンテナンス頻度の削減が見込めます。さらに膜厚方向に組成制御が可能で、エージング時間を短縮することができるので、装置稼働率の向上が見込まれます。
成膜方法については、緻密性、厚膜性においてIon Assist蒸着法(IAD)が優れています。当社の技術は世界初の酸素イオン照射による緻密で10μm以上のY₂O₃成膜に成功しました。
成膜方法については、緻密性、厚膜性においてIon Assist蒸着法(IAD)が優れています。当社の技術は世界初の酸素イオン照射による緻密で10μm以上のY₂O₃成膜に成功しました。
Ion Assist蒸着で世界初の酸素イオン照射による緻密で10μm以上のY₂O₃成膜が可能となりました。
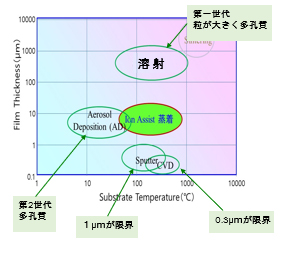
従来の成膜方法との比較
従来の成膜方法との比較
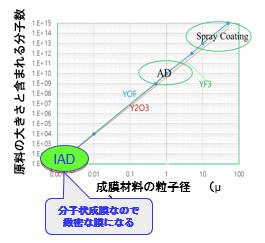
原料粉が細かければ膜も緻密になる→分子状成膜:最も緻密
原料粉が細かければ膜も緻密になる→分子状成膜:最も緻密
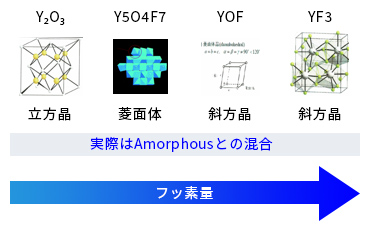
安定相は4相:F量と膜硬度は反比例
安定相は4相:F量と膜硬度は反比例
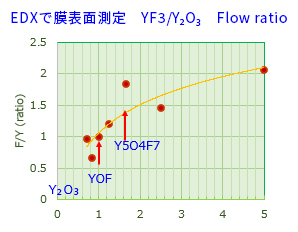
流量比で制御可能
流量比で制御可能
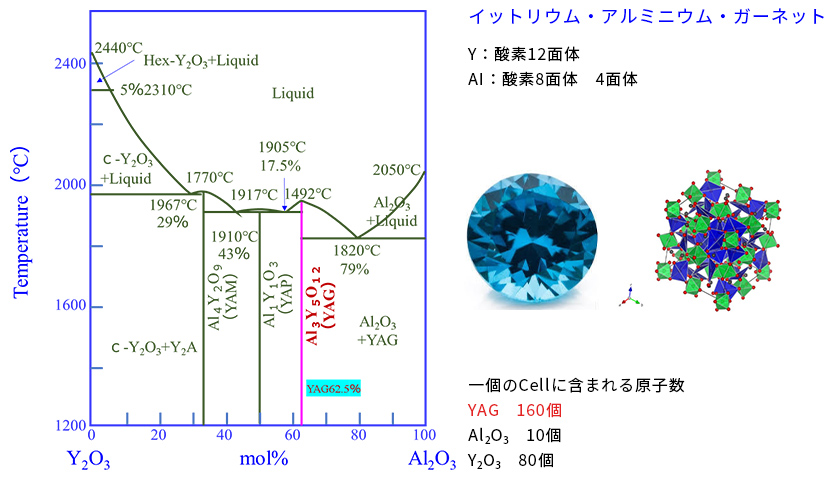
複雑な構造:硬度が2000MPa以上
複雑な構造:硬度が2000MPa以上
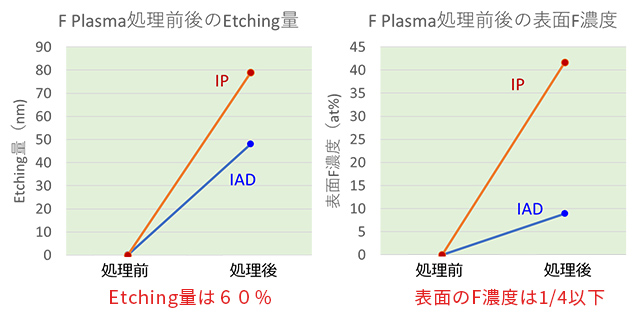
F Plasma耐食性が大幅に向上
F Plasma耐食性が大幅に向上
超緻密膜、かつ(111)最稠密面に優先配向する為フッ素プラズマに対して大きな耐食性を示す

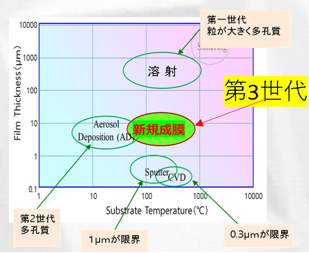
従来の成膜方法との比較
従来の成膜方法との比較
IAD膜
|
従来のIon Plating
|
|
Plasma
処理前 |
![]() |
![]() |
F-Plasmaで表面形状が少し変化
|
大幅に変質
|
|
Plasma
処理後 |
![]() |
![]() |
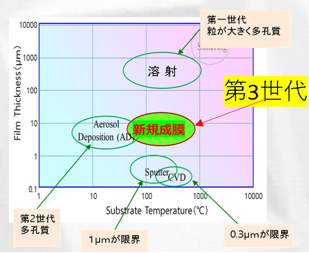
従来の成膜方法との比較
従来の成膜方法との比較
Oxide
|
ΔG0f
|
Floride
|
ΔG0f
|
沸点
|
kJ/mol
|
kJ/mol
|
℃
|
||
SiO2
|
-857
|
|||
TiO2
|
-890
|
|||
Fe3O4
|
-1015
|
FeF2
|
-1162
|
<1000
|
Cr2O3
|
-1058
|
CrF2
|
-732
|
1300
|
MgO
|
-1170
|
MgF2
|
-1070
|
2260
|
Al2O3
|
-1582
|
AlF3
|
-1425
|
1260
|
La2O3
|
-1706
|
|||
Y2O3
|
-1727
|
YF3
|
-1645
|
2200
|
Ta2O5
|
-1911
|
TaF5
|
融点97℃
|
|
Ti2O5
|
-2318
|
TiF4
|
融点377℃
|
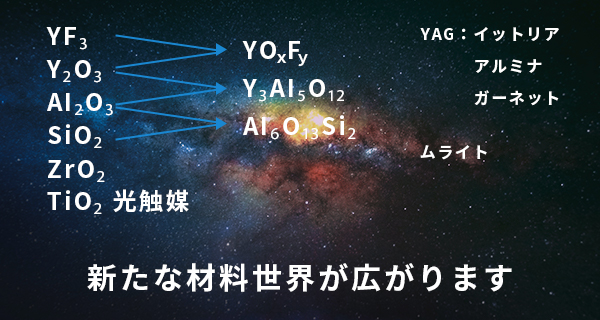
その他の対応可能な材料・成膜
アルミ表面粗化(アルマイト) 概要
照明機器の高輝度LED化や電子機器の高機能·高性能化に伴い、 電子部品からの発熱は増大の一途を辿っている。
その熱対策として、 多くの電子部品を搭載するプリント配線基板には、高熱伝導率の絶縁樹脂の採用や、プリント回路基板と金属板を一体化させ、熱を逃がす手法やなどが用いられている。
金属板には、熱伝導性に優れ、軽量かつ低コストであるアルミニウムが広く利用されている。
しかしながら、絶縁樹脂との接着性に乏しいことから、基板加工時や加熱処理において剥離を発生する場合があり、より強固な接着が求められている。また、金属板に伝熱された熱の放熱性についても改善する必要がある。
その熱対策として、 多くの電子部品を搭載するプリント配線基板には、高熱伝導率の絶縁樹脂の採用や、プリント回路基板と金属板を一体化させ、熱を逃がす手法やなどが用いられている。
金属板には、熱伝導性に優れ、軽量かつ低コストであるアルミニウムが広く利用されている。
しかしながら、絶縁樹脂との接着性に乏しいことから、基板加工時や加熱処理において剥離を発生する場合があり、より強固な接着が求められている。また、金属板に伝熱された熱の放熱性についても改善する必要がある。
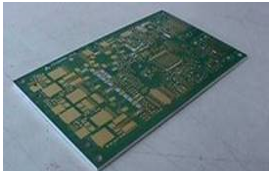
車載基板(3tAL+高熱伝導樹脂4層基板)
車載基板(3tAL+高熱伝導樹脂4層基板)
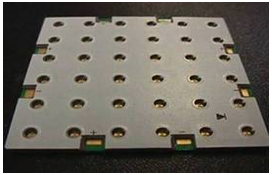
LED照明基板(2.0tAL+FR-4.4層基板)
LED照明基板(2.0tAL+FR-4.4層基板)
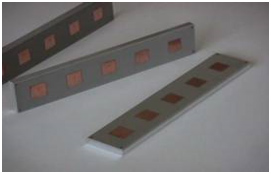
アンテナ基板(5tAL+フッ素樹脂両面基板)
アンテナ基板(5tAL+フッ素樹脂両面基板)
理想とした粗化形状
現状の表面状態から見た樹脂との接着イメージ
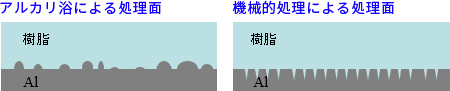

理想の改良型アンカーイメージ
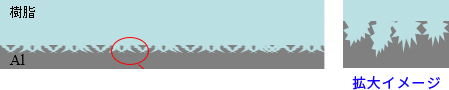
アルマイト膜を利用した高熱伝導プリント回路基板
熱は電子機器の安全性と性能、そして信頼性に悪影響を及す
■発煙,発火の危険性
■動作速度の低下や動作不良,
■デバイスの故障や電子機器の短寿命化
一般基板と高熱伝導基板の違い
|
|||
一般基板
|
![]() |
![]() |
パワー部品で発生した熱は、導体を通じ絶縁層へ伝熱していくが、樹脂の放熱性が低いため基板温度は上昇。
|
メタル付き基板
|
![]() |
![]() |
絶縁層に熱伝導率の高い樹脂材料を用い、発熱した熱を樹脂層を介し、熱伝導率の大きい金属(ALやCu)へ伝熱させ放熱。
|
ダイヤモンド成膜
素材
|
密着性(感覚)
|
シリコン(Si)
|
◎
|
炭化ケイ素(SiC)
|
◎
|
ダイヤモンド
|
◎
|
窒化ケイ素(Si3N4)
|
◎
|
アルミナ(Al203)
|
△
|
Ti合金
|
×
|
ニオブ(Nb)
|
○
|
銅(Cu)
|
×
|
モリブデン(Mo)
|
○
|
超硬(WC)
|
○
|
石英(SiO2)
|
×
|
ガリウムナイトライド(GaN)
|
×
|
SUS
|
×
|
鉄
|
×
|
アルミニウム
|
×
|

摺動
|
■耐摩耗性における改善膜
セラミック材料への成膜実績有(炭化珪素など) 軸受け、メカニカルシールなどへ適応されている |
電極
|
■導電性ダイヤモンド膜の作成 (ボロンドープダイヤモンド膜)
オゾン発生、CO₂還元用の電極 OHラジカルの生成やホルムアルデヒドの生成など |
半導体試作
|
■半導体及び試作内容
・半導体用途 ・ダイヤモンド膜の平坦化加工 ・低温合成 ・任意形状へのダイヤモンド成膜 ・単結晶ダイヤモンド成長 |
金型
|
■ダイヤモンド金型 (ダイヤモンド自立体の作製)
マイクロンレンズアレー レンズ金型など 形状形成基板へダイヤモンド膜を成長 |
環境対策
・プラスティックの代替として撥水コーティングした生分解性材料の開発
・海洋汚染のマイクロプラスティック削減
・海洋汚染のマイクロプラスティック削減
基材の例
|
|
紙
|
和紙、洋紙、機能紙、一般的に紙と呼ばれているもの等
|
繊維
|
綿毛、麻、絹、カーボン、無機繊維等
|
付与できる性質
|
説明
|
耐水性
|
シロキサン結合による薄膜が基材の表面を造膜し、優れた耐水性を発揮します。
また、撥水性の度合いについては自由に変えることができます。 |